A lo largo de mi tiempo en el mercado flexográfico he estado involucrado continuamente en investigación, capacitación, resolución de problemas y proyectos para revolucionar la industria. A veces los resultados son pequeños, a veces grandes, a veces aceptados, pero la mayoría de las veces resistidos. La mayoría de las veces la respuesta cuando pregunto «¿Por qué haces eso?» es «¡porque siempre lo hemos hecho!»
Después de un tiempo adquieres los mismos hábitos, y sin darte cuenta terminas en el mismo modo de “eso es normal en flexografía” y aceptando algunas cosas que realmente no deberías. ¡Todos lo hacemos! Un ejemplo que me viene a la mente es “Tengo que elegir entre buenas mechas o buenos sólidos, no puedo tener ambas!” Esto se debe a la típica naturaleza porosa de los sólidos en flexografía y a las cuatro acciones principales que las personas toman para solucionarlo:
- Aumente la cantidad de tinta utilizada con mayores volúmenes de rodillo anilox
- Aumenta la fuerza de la tinta con más pigmento.
- Aplique más presión de impresión desde la placa al sustrato.
- Separe las pantallas (resaltados) y los sólidos en dos placas separadas para ese color
Sin embargo, cuando analizamos cada una de estas cuatro acciones “normales” en flexografía, debido a la necesidad de elegir entre luces y sólidos, vemos los verdaderos resultados:
1. ¡MÁS TINTA! Agregar más tinta no elimina los poros en el sólido, sino que aplica crestas de tinta más grandes a la superficie del sustrato. Más tinta significa más materias primas, más solvente para eliminar durante el secado; Más secado significa más energía en forma de calor. Una mayor energía del secador a menudo significa que es necesario reducir la velocidad de la prensa para lograrlo, lo que resulta en una pérdida de productividad. Todas estas son acciones “normales” en flexografía, que resultan en más materias primas, más energía, mayores costos y menor productividad.
Otros problemas con el uso de más tinta es que tiende a causar más impresión sucia, lo que provoca más paradas para limpiar las planchas y aumenta el riesgo de dañar las planchas. Esto supone un coste en tiempo, productividad y materiales, pero da como resultado una calidad de impresión inconsistente y, a menudo, afecta negativamente a los procesos posteriores, como la laminación y el corte/conversión, cuando es necesario retirar los materiales. Una acción “normal” comúnmente aceptada para reducir el riesgo de impresión sucia es reducir la resolución aplicada, como LPI, haciendo que los puntos mínimos sean más grandes y disminuyendo las capacidades de calidad de la imagen.
2. ¡MÁS PIGMENTO! El pigmento es el componente de la tinta que proporciona el color que buscamos, y la teoría es utilizar más pigmento para obtener más color. Pero cuando la tinta se aplica en crestas separadas por orificios, el efecto y el valor se minimizan. La mejor manera de obtener el color más fuerte y limpio es una capa fina y uniforme de pigmento sin poros, ¡más parecido a lo que vemos tradicionalmente en la impresión en huecograbado! Luego, la luz se refleja de manera más uniforme, dando un color más limpio, brillante y fuerte.
El pigmento es uno de los componentes más caros, si no el más caro, de la tinta, por lo que agregar más aumenta significativamente los costos. Además, si sigues agregando pigmento, la densidad aumenta hasta llegar a un punto en el que interfiere con el flujo de tinta y puede hacer que la densidad disminuya. La mayoría de las tintas flexográficas están pigmentadas al máximo, a menudo más allá del valor óptimo para una impresión eficiente. El flujo de tinta es un factor crítico, especialmente a medida que aumenta la velocidad de la prensa, y un flujo deficiente de tinta provocará falta de tinta y malos sólidos.
Esto también puede causar un aumento de la impresión sucia, de manera similar a un mayor volumen de tinta en la primera acción, con soluciones similares para abordarlo, lo que resulta en mayores costos, menor productividad y menor calidad de imagen.
3. ¡MÁS PRESIÓN DE IMPRESIÓN! Esto es algo que todos los impresores flexográficos del mundo parecen saber: cuando se aplica más presión de impresión desde la plancha al sustrato, ¡la densidad aumenta!
Cuando preguntas por qué, no muchos pueden explicártelo, ¡pero saben que simplemente funciona! La explicación para esto es realmente muy simple: la tinta se aplica en crestas separadas por orificios o huecos; y a medida que aplica más presión en la parte superior de la cresta, la tinta se aplasta hacia los lados, llenando los huecos y aumentando la cobertura de tinta, ¡y aumentando la densidad lograda!
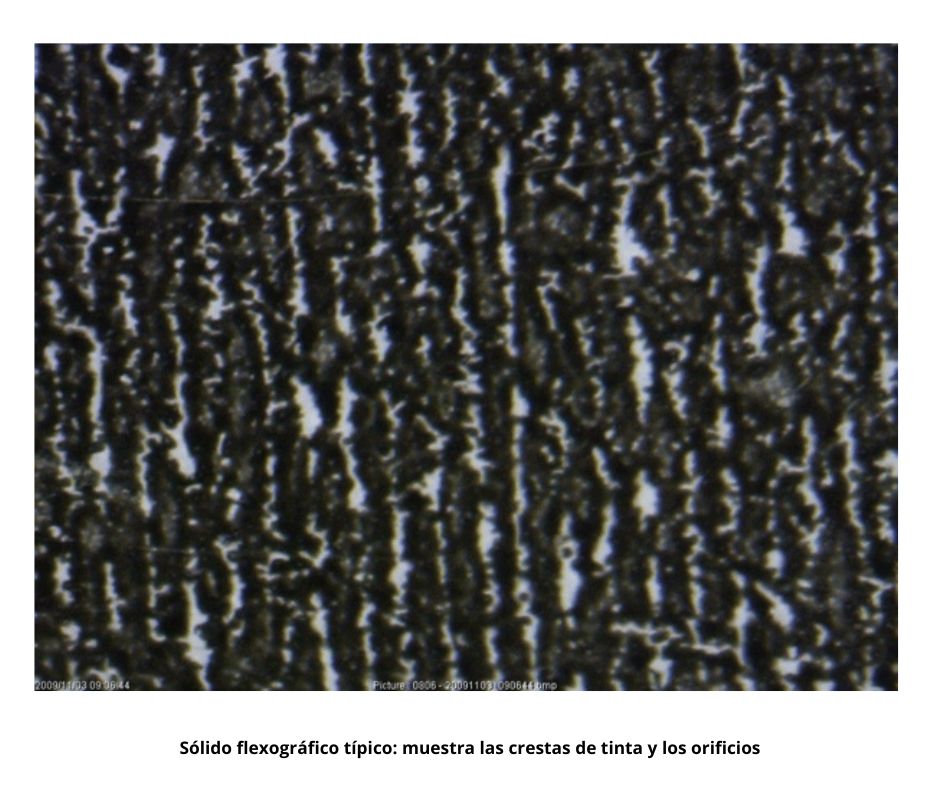
Desafortunadamente, la mayoría también trabaja según el principio de que «si un poco más de presión de impresión es bueno, entonces mucha más debe ser mejor». Esto da como resultado una impresión excesiva y eso introduce una serie de problemas completamente nuevos.
La sobreimpresión provoca una ganancia excesiva de puntos en las luces, un desgaste acelerado de la plancha en las luces y acumulación de tinta que provoca impresiones sucias. Si bien es cierto para los puntos superiores planos y redondos, los problemas son particularmente ciertos para los puntos superiores redondos del LAMS (Sistema de máscara ablativa por láser) digital tradicional, donde el área de superficie muy pequeña es muy sensible a la presión, crece rápidamente y causa un exceso. calor y fricción para desgastar los puntos más pequeños. Este desgaste acelerado, junto con la sensibilidad a la impresión de las planchas LAMS tradicionales, provoca una mayor sensibilidad del operador e inconsistencia en la configuración y durante el proceso.
La sobreimpresión también tiende a expulsar más la tinta de los puntos más pequeños hacia los bordes, lo que provoca que se acumule la tinta y resulte en una impresión sucia. Esto significa entonces más paradas para limpiar las placas y eso aumenta el riesgo de dañar las placas. Aumentar el tamaño mínimo de punto puede ayudar: con un LPI más bajo para la imagen, los puntos más grandes son menos sensibles, tienden a ser más planos en la parte superior y distribuyen mejor la impresión. Pero hacer esto es una clara señal de aceptar que es normal comprometer lo más destacado para mejorar los sólidos.
4. ¡DIVIDIR SÓLIDOS Y PANTALLAS! Esto es realmente una señal de que tienes que tirar la toalla y aceptar que, en lugar de uno u otro, necesitas obtener lo mejor de ambos mundos. Esta es una acción normal con las placas LAMS tradicionales con su parte superior redondeada y, con menos frecuencia, con las soluciones digitales de punto plano. Esto significa más preimpresión: dos planchas, dos cintas de montaje, dos tintas, dos estaciones de impresión que configurar, dos secadores que ejecutar, etc. Básicamente, más materiales, más energía, por lo tanto, más costos. Una cosa a su favor es que hacer esto significa que la plancha sufre menos falta de tinta y problemas de secado, y a menudo funciona más fácil y más rápido con las planchas LAMS tradicionales.
Estas cuatro acciones son “normal” y aceptados como necesarios en toda la flexografía, y en el pasado a menudo eran necesarios. Sin embargo, hoy esto no es cierto.
Preguntas y Respuestas:
1. ¿Cuáles son algunas de las acciones «normales» en flexografía que el artículo cuestiona como no deseables y por qué?
Las acciones comunes cuestionadas incluyen el aumento de la cantidad de tinta, el incremento del pigmento, la aplicación de más presión de impresión y la separación de sólidos y pantallas. Estas prácticas llevan a resultados ineficientes, mayor costo en materias primas, energía y menor productividad.
2. ¿Cuáles son las implicaciones de agregar más tinta en el proceso de flexografía?
Añadir más tinta no resuelve la porosidad en los sólidos; en su lugar, genera crestas de tinta más grandes en el sustrato. Esto conlleva a mayores costos de producción, impresiones sucias que requieren limpieza frecuente de las planchas y una calidad de impresión inconsistente.
3. ¿Por qué el aumento del pigmento no es una solución efectiva?
A pesar de buscar colores más intensos, el incremento de pigmento conduce a una aplicación irregular en el sustrato por la naturaleza porosa de la flexografía. Esto resulta en mayores costos de tinta, flujo deficiente que afecta la calidad de impresión y también contribuye a problemas de impresión sucia.
4. ¿Cómo afecta la aplicación excesiva de presión de impresión al proceso de flexografía?
Aplicar más presión aumenta la densidad de la tinta, pero también genera problemas como ganancia excesiva de puntos en las luces, desgaste rápido de las planchas, acumulación de tinta y problemas de impresión sucia. La sobreimpresión causa daños en los puntos más pequeños y disminuye la consistencia en el proceso.
5. ¿Cuál es la alternativa propuesta para mejorar la calidad en flexografía?
buscar una capa delgada y uniforme de pigmento, similar a la técnica de impresión en huecograbado. Esto permitiría una reflexión de luz más uniforme, colores más limpios y fuertes sin comprometer la calidad de la imagen.
Cómo Mejorar la Eficiencia Industrial con Actuadores Inteligentes: Guía para Empresas que Buscan Automatización
Actuadores Lineales vs. Rotativos: ¿Cuál Elegir para Automatizar Rodillos Industriales?
Tipos de Actuadores en la Automatización Industrial: Guía Completa para Seleccionar el Ideal
En el mundo de la automatización industrial, los actuadores son componentes fundamentales para transformar señales…
Control de Precisión en Sistemas Eléctricos Automatizados: Clave para la Eficiencia Industrial
Cómo Integrar Actuadores Hidráulicos y Neumáticos en la Automatización Industrial
Comparativa: Sistemas Hidráulicos vs. Neumáticos vs. Eléctricos en Automatización Industrial
En la industria moderna, la automatización de procesos es esencial para alcanzar mayores niveles de…